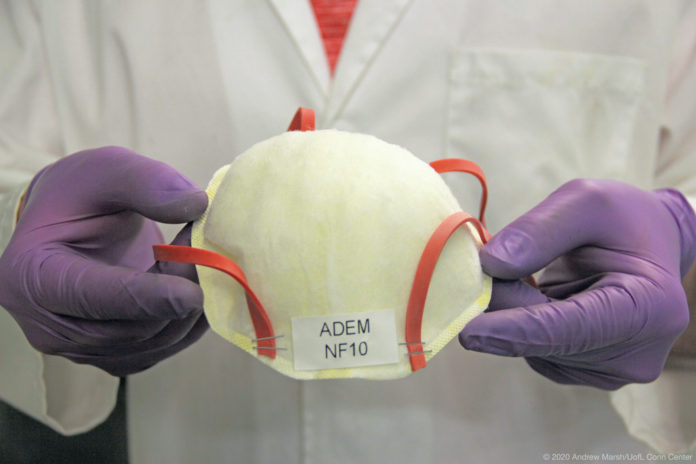
Scientists at the University of Louisville’s Conn Center for Renewable Energy Research and the Advanced Manufacturing Institute of Science & Technology (AMIST) have partnered with Advanced Energy Materials, LLC (ADEM) to develop and patent a more effective and reusable N95 mask to filter COVID-19 droplets and other airborne particles and viruses.
The masks are being developed using nanomaterial research at the Conn Center, a J.B. Speed School of Engineering center that usually focuses on commercializing innovations in solar energy storage, biofuels, solar fuels and energy efficiency. Researchers saw an opportunity to use their innovative work to help provide low-cost, effective personal protective equipment (PPE) for health care workers.
Unlike currently available N95 masks, which cannot be reused without special decontamination procedures, these cost-effective nanofilter masks can be easily washed, dried and reused.
They are made using inorganic nanowires impregnated into a woven polymer cloth with a minimum efficiency reporting value (MERV) of 15 that together form a porous network whose openings are too small for viral particles to pass through. Current N95 masks rely on an electrostatic charge on polymer fiber cloth to capture nuisance particles such as dust, mold and pollen. This method may not be effective with liquid droplets or viral pathogens and doesn’t offer any disinfection capabilities.
The titania and zinc oxide nanowire materials that form the nanofilter are also capable of absorbing ultraviolet (UV) light, a benefit of their adoption from the renewable energy research at Conn Center. The filters can be disinfected using a low energy UV light source, helping to reduce PPE costs in hospitals.
The partnership includes Ed Tackett, director of workforce development at AMIST, and chemical engineering Professor Mahendra Sunkara, director of the Conn Center. Sunkara co-founded ADEM in 2010 with his wife, CEO Vasanthi Sunkara, to scale up energy materials innovations from his work at the university.
Since then, ADEM has scaled up manufacturing of nanowire materials from grams at a time to ton scale. “Producing bulk quantities is a considerable challenge in translating a new material from laboratory to marketplace,” Mahendra Sunkara said. “In the lab, we only make very small amounts to test and study, but tons per day are required for meeting commercial demand.”
Tackett and Sunkara realized a growing PPE challenge as the COVID-19 pandemic has unfolded.
“How do we as Kentucky respond to multiple waves of disease and low case rate due to success of ‘stay safe’ measures?” Tackett said. “We are all working together to keep the rate of incidence low, but that also means we will have difficulty in priority purchasing for PPE since Kentucky isn’t a hotspot. Our solution is making them here instead of buying elsewhere.”
The manufacturing method for the masks is adopted from Conn Center’s roll-to-roll printing techniques used in battery electrode and solar cell fabrication. The availability of materials at quantity and adapted expertise made this nanofiltered cloth innovation possible.
“The shortage of protective gear during this pandemic has made us rethink our strategy to utilize ADEM’s nanowire materials for PPE,” said Vasanthi Sunkara. “It just shows that with the right connections, expertise and resources, the university and industry can come together quickly to move innovation through manufacturing and into the market to affect this challenge head-on.”
Prototype testing on the nanofilters is underway. Once validated, the next steps are to set up manufacturing in two types of facilities. The first is a large-scale, roll-to-roll printing operation for making the nanofilter cloth. The second is a forming and assembly line to make flat filters and ready-to-wear N95-style respirators.
ADEM in conjunction with Conn Center will produce both flat filters and respirators right away. The center can produce thousands over the next two months until automated production equipment is put in place for mass production at several million per year. AMIST and the Kentucky Cabinet for Economic Development are looking at what is needed to build the mask-making capacity for Kentucky.
Funding for this phase has been made possible by Hank and Rebecca Conn, benefactors of the Conn Center. The gift is intended to be matched by donors who want to help during the COVID-19 crisis.
“It is the right thing to do,” said Hank Conn. “Conn Center technologies are intended for renewable energy but can impact the immediate health crisis. We are giving this innovation early support that it may reach a commercialization partner for the good of us all.”