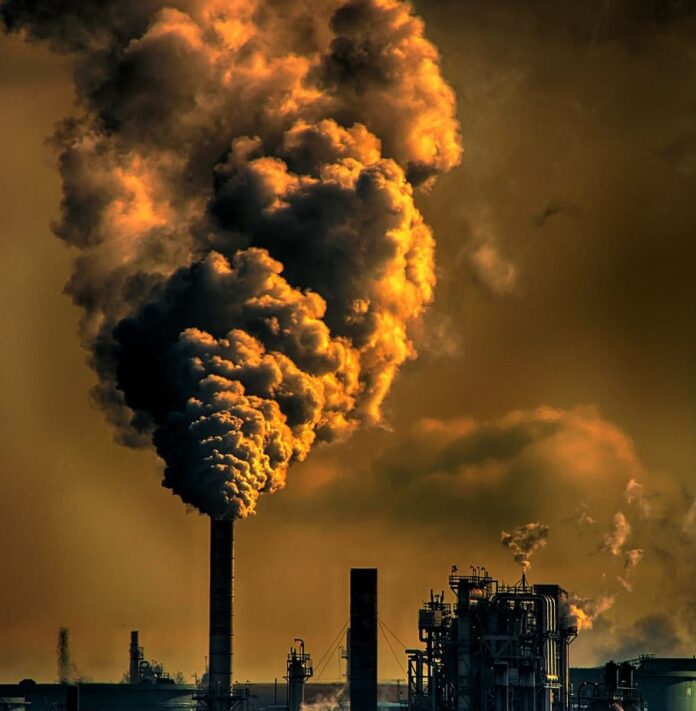
Researchers at the University of Louisville Conn Center for Renewable Energy Research and Department of Chemistry are working to convert the greenhouse gas carbon dioxide into valuable products. U.S. Department of Energy funding has been awarded for “Electrochemical Reduction of Flue Gas CO2 to Commercially Viable C2 – C4 Products,” a project to convert waste CO2 into two- to four-carbon (C2-C4) chemicals through an electrochemical reduction route.
Earth depends on balanced levels of greenhouse gases for our warm climate, averaging 59oF, to sustain plant and animal life. Since the Industrial Revolution, burning of fossil fuels for energy has resulted in the excessive accumulation of atmospheric gases such as CO2, raising the temperature of the planet.
Greenhouse gas levels are the highest ever recorded and continue to rise as worldwide energy use is projected to double in the next 10 years. Flue gas is the smoky exhaust from a furnace, boiler or generator and, on a larger scale, the gas that results from combustion at power plants. A major portion of U.S. greenhouse gas emissions (approximately 33%) are attributable to the flue gas resulting from electricity generation by utilities.
While most research into electrochemical reduction of carbon dioxide has relied on pure gas feedstocks, CO2 is more dilute in flue gas at typically less than 20%. The Conn Center project will pursue the development of a stable and efficient method to convert the CO2 directly from a power plant exhaust stream, which would aid in making the overall process more cost-effective.
Flue gas contaminants can degrade the performance of an electrolysis reactor, making the direct electrochemical conversion of flue gas CO2 a challenging prospect. The UofL team is working on novel molecular catalysts to guide the selectivity of the reaction within a new high-performance reactor designed for use with both water and organic solvent.
The major challenge of utilizing flue gas CO2 to produce carbon-based chemicals is to create technology that is efficient, economical and achievable at a commercial scale. Meeting these three criteria would provide an economic incentive for industry by adding value to their waste instead of emitting it to the atmosphere.
These power plant emissions will be processed to convert CO2 to useful products, including those where the single carbon atoms in CO2 are combined to form larger compounds with two to four carbon atoms. Such products include formic acid, ethanol and methyl formate, all of which are currently produced using fossil fuels.
The research team is led by Joshua Spurgeon, Ph.D., theme leader for Solar Fuels at the Conn Center for Renewable Energy Research in the J.B. Speed School of Engineering, and UofL chemistry professor Craig Grapperhaus, Ph.D., in conjunction with the University of North Dakota’s Institute for Energy Studies. This research has been funded by the U.S. Department of Energy (DOE) National Energy Technology Laboratory (NETL). Funding of $1.25 million over two years was secured by Spurgeon and Grapperhaus to conduct the research, which has enabled the recruitment of several graduate students and postdoctoral scholars and will include research opportunities for undergraduate students.
The partnership also includes an alumnus of the University of Louisville Speed School. Nolan Theaker, one of Spurgeon’s previous undergraduate researchers, is now a Ph.D. student at the University of North Dakota and a research engineer with the Institute for Energy Studies. Theaker will lead the effort at UND to develop methods to process the flue gas for stable and efficient operation in the electrolyzer. This partnership includes Minnkota Power Cooperative, which will provide access to its coal-based post-combustion flue gas and analysis capabilities.
Spurgeon and Grapperhaus designed this project based on their published preliminary data from similar research on electrochemical conversion of CO2, including Spurgeon’s work on electrochemical CO2 reactors and Grapperhaus’s work on molecular catalysts, which bind CO2 and assist the conversion. In the new effort, they will pursue a high-performance reactor design capable of meeting the metrics necessary for a commercially viable process. This includes achieving much higher operating current densities, similar to water-based electrolyzers, than typical laboratory measurements and very high selectivity (~90%) for the desired chemical products.
“Electrochemical reduction of CO2 allows for renewable energy-driven production of chemicals and fuels in a distributed and modular fashion,” said Mahendra Sunkara, director at Conn Center. “Conn Center is looking towards the development of a CO2 electrolyzer in the next five years.”